
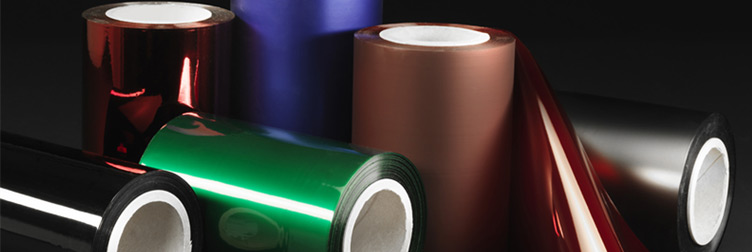
行业应用
超高分子量聚乙烯(UHMWPE)是粘均分子量在150万以上的线形结构聚乙烯(普通聚乙烯的相对分子质量仅为2-30万)。极高的相对分子量,赋予了其超凡的使用性能,成为一种性能优良的新型热塑性工程塑料。由于其分子量极高,它几乎集中了各种塑料的优点,具有普通聚乙烯和其他工程塑料所无可比拟的耐腐、耐冲击、自润滑、耐腐蚀、耐低温、卫生无毒、不粘附、不吸水等综合性能。在固体颗粒、粉末、浆体、气体输送方面,有独一无二的优越性。被称为“令人惊异的塑料”。 近年来由于柱塞推压、单螺杆挤出等技术的突破,使超高分子量聚乙烯管材在国内也实现了工业化连续生产。但由于超高分子量聚乙烯原料的特性决定了超高分子量聚乙烯管材加工的难度,虽然超高分子量聚乙烯管材生产实现了塑料挤出机连续挤出生产,可它的生产速度仅为普通塑料管材制品生产速度的1℅,管材耐磨指标也仅能达到西欧发达国家管材制品耐磨指标的60℅左右,提高超高分子量聚乙烯管材生产速度和提高耐磨指标成为业界研究的重点。 近几年,超高分子量聚乙烯管材的应用范围日益扩大。正因为超高分子量聚乙烯管具有耐摩擦、耐腐蚀、抗冲击、自润滑、不粘附、不吸水、等优良特性。市场认知度逐步提高。 现在大部分工厂生产超高分子量聚乙烯管材生产工艺还是沿用前人开发的老设备、老工艺。效率低、能耗大、生产速度慢,且生产的超高分子量聚乙烯管材制品外观质量及内在质量都很差,完全丧失了超高分子量聚乙烯管材应有的内在质量。 生产超高分子量聚乙烯管材的主要设备塑料挤出机大部分生产厂家采用单螺杆挤出机,螺筒螺杆材质为38CrMoALA,螺杆螺纹形式为单头渐变式,管材成型为模具冷却定型,模具冷却方式最早为“风冷式”,后来发展为“水冷式”。这两种方式现在在各个生产企业还在继续沿用。 此新工艺是在国内国外专门研究超高分子量聚乙烯管材生产工艺的各位前辈研究的基础上,总结了 国内数十个生产厂家及使用单位在生产及使用的对比数据,通过一系列生产、试用实验得来。 实验结论是,通过调整超高分子量聚乙烯管材生产设备的配置及其工艺方法,能有效的提高超高分子量聚乙烯管材生产速度,大幅度的提高超高分子量聚乙烯管材的内在质量及其外观质量。 新工艺采用超高分子量聚乙烯管材生产的主要设备为单螺杆挤出机,螺筒螺杆材质为38CrMoALA,螺杆螺纹形式为为双头渐变式,螺距为75 --200mm不等,配置动力为15--55KW不等,管材成型为模具冷却定型,但即不是“风冷模式“,也不是“水冷模式”,而是“水冷油→油冷模式”(具体冷却方式详见后图示)。 “风冷模式”的主要缺点是因为通过风机对管材模具的成型末端的内外壁进行冷却定型,冷却速度慢,管坯成型差,管材制品得不到快速有效的冷却定型,挤出速度缓慢(平均3cm/min),管材内外壁密实度不好,管材表面没有光亮度,所以管材耐磨效果不好;“水冷模式”相比“风冷模式”所生产的制品在制品质量及生产线速度上均有一定程度的提高,但它的主要缺点是因为大多数的厂家模具冷却水没有通过水处理,而水在100℃时就达到沸腾点,,且产生大量水垢,水垢会堵塞冷却流道,使整个模具无法使用;水的100℃时的沸腾点也限制了模具的热量传导【超高分子量聚乙烯管材正常生产时模具温度一般在200℃左右】,导致一些特种制品不能有效冷却。 “水冷油→油冷模式”与之相比优点是相比前两种方式,超高分子量聚乙烯管材制品产量能提高一倍以上,所生产管材制品表面能达到“镜面”效果。全面提高超高分子量聚乙烯管材耐磨、防结蜡的独特的优势。其具体方法为:企业自备水箱(或自来水)→油箱内置冷却盘管(盘管被完全浸泡)→返回企业自备水箱;油箱内被冷却到一定温度的冷却油用动力输送到模具,冷却模具后返回油箱,循环往复。 因为超高分子量聚乙烯管材生产线速度慢,所以一般生产厂家在管材成型后会直接让管材上托架,达到需求长度后再切断、堆放、打包、入库。采用本工艺后,因为有效的提高了管材生产的线速度(针对小规格管材¢50—100mm),可在模具后端加冷却水箱,小型牵引机,自动切割机,堆放架等装置,可相辅相成,更能提高产品生产速度及管材质量。 |